Understanding Plastic Injection Molders: An In-Depth Analysis
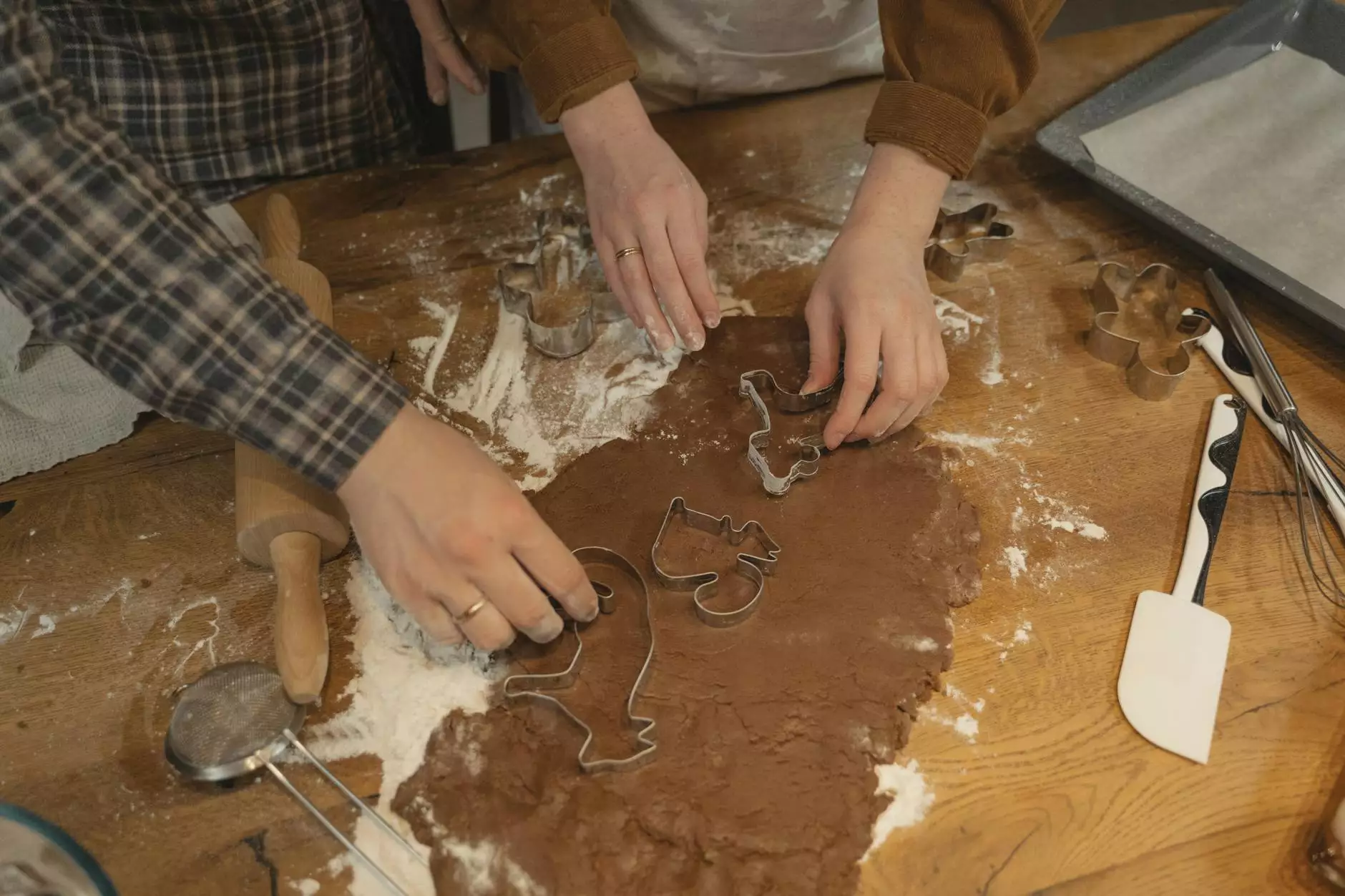
The manufacturing landscape has evolved significantly, particularly with the introduction of plastic injection molders. These devices have revolutionized the way we produce plastic products, offering efficiency, precision, and the ability to customize designs like never before. In this article, we will delve into the intricacies of plastic injection molding, its processes, benefits, and its essential role in modern manufacturing.
What Are Plastic Injection Molders?
Plastic injection molders are machines used in the process of shaping plastic materials by melting and injecting them into molds. This method is prevalent in producing a wide variety of plastic goods, from automotive parts to household items. The versatility and efficiency of these machines make them an integral part of the manufacturing sector.
The Injection Molding Process
The process of injection molding can be broken down into several critical stages:
- Material Selection: The first step involves choosing the right type of plastic material. Most commonly, thermoplastics are used, which can be melted and molded multiple times.
- Extrusion: The plastic material is fed into a heated barrel where it is melted down to a viscous state.
- Injection: The molten plastic is injected into a mold under high pressure. This pressure is crucial for ensuring that the plastic fills every cavity of the mold accurately.
- Cooling: Once injected, the material is allowed to cool and solidify, taking the form of the mold.
- Ejection: After cooling, the mold opens, and the newly-shaped plastic component is ejected, ready for any finishing processes.
Benefits of Using Plastic Injection Molders
Utilizing plastic injection molders brings numerous benefits to manufacturers:
- Efficiency: High production rates mean that large volumes of parts can be produced in a relatively short time.
- Precision: The process allows for high accuracy in the dimensions and appearances of the final products.
- Cost-Effectiveness: Especially in large-scale production, the cost per unit decreases significantly.
- Complex Shapes: Injection molding can produce intricate designs that would be challenging with other manufacturing methods.
The Role of Metal Fabricators in Manufacturing
While plastic injection molders focus primarily on plastic materials, the role of metal fabricators is essential in the overall manufacturing ecosystem. Here’s how:
- Production of Molds: Metal fabricators are often responsible for creating the molds used in the injection process. These molds must be durable and precise to withstand the pressure of injection and the heat of molten plastic.
- Component Fabrication: In addition to molds, metal fabricators produce various components that may be required for assembly with plastic parts.
- Maintenance and Repair: Fabricators also provide essential services in maintaining and repairing molds, ensuring they remain in optimal condition for production.
Types of Plastic Injection Molding
There are several types of plastic injection molding techniques, each with its specific advantages:
1. Conventional Injection Molding
This is the most common form, ideal for large production runs. It is characterized by high speed and efficiency.
2. Thin-Wall Injection Molding
Used for products that require a minimal wall thickness, this method optimizes the material and production cost.
3. Insert Molding
This technique involves inserting a component (typically metal) into the mold before injecting the plastic. It is often used in electronics and automotive parts.
4. Overmolding
This process creates a two-material product by molding a second type of plastic over a substrate, allowing for improved grip and aesthetics.
5. Structural Foam Molding
This method uses a combination of foamed and solid material, resulting in lightweight yet strong parts.
Quality Control in Plastic Injection Molding
Implementing quality control measures is critical in the injection molding process. High-quality parts are necessary for maintaining customer satisfaction and reducing costs associated with defects. Some techniques include:
- Material Testing: Ensuring the plastic material meets required specifications before production.
- Dimensional Inspection: Regularly checking the dimensions of produced parts using precise measuring equipment.
- Operational Checks: Monitoring the injection process to ensure that temperatures and pressures are within acceptable limits.
- Final Part Assessment: Conducting thorough inspections of the completed products for aesthetic and functional defects.
The Future of Plastic Injection Molding
The future of plastic injection molders appears promising. Innovations in technology and materials are shaping the landscape:
1. Sustainable Practices
With increasing environmental concerns, manufacturers are exploring bioplastics and recycled materials to create more sustainable products.
2. Automation and Smart Technologies
Integrating AI and automation into the injection molding process allows for real-time monitoring, reducing downtime, and increasing efficiency.
3. Advanced Mold Design
New mold designs are emerging that allow for complex geometries and improved thermal management to enhance production outcomes.
Conclusion: The Importance of Plastic Injection Molders
In conclusion, plastic injection molders play a vital role in the manufacturing sector, providing efficiency, precision, and cost-effectiveness. Understanding the intricate processes involved, the benefits offered, and the future trends will enable manufacturers to thrive in an ever-evolving market.
As we move forward, the collaboration between plastic injection molders and metal fabricators will remain crucial to producing high-quality products that meet the demands of consumers and industries around the world. Embracing new technologies and sustainable practices will pave the way for a more innovative and responsible manufacturing future.