Understanding Pressure Die Casting Components
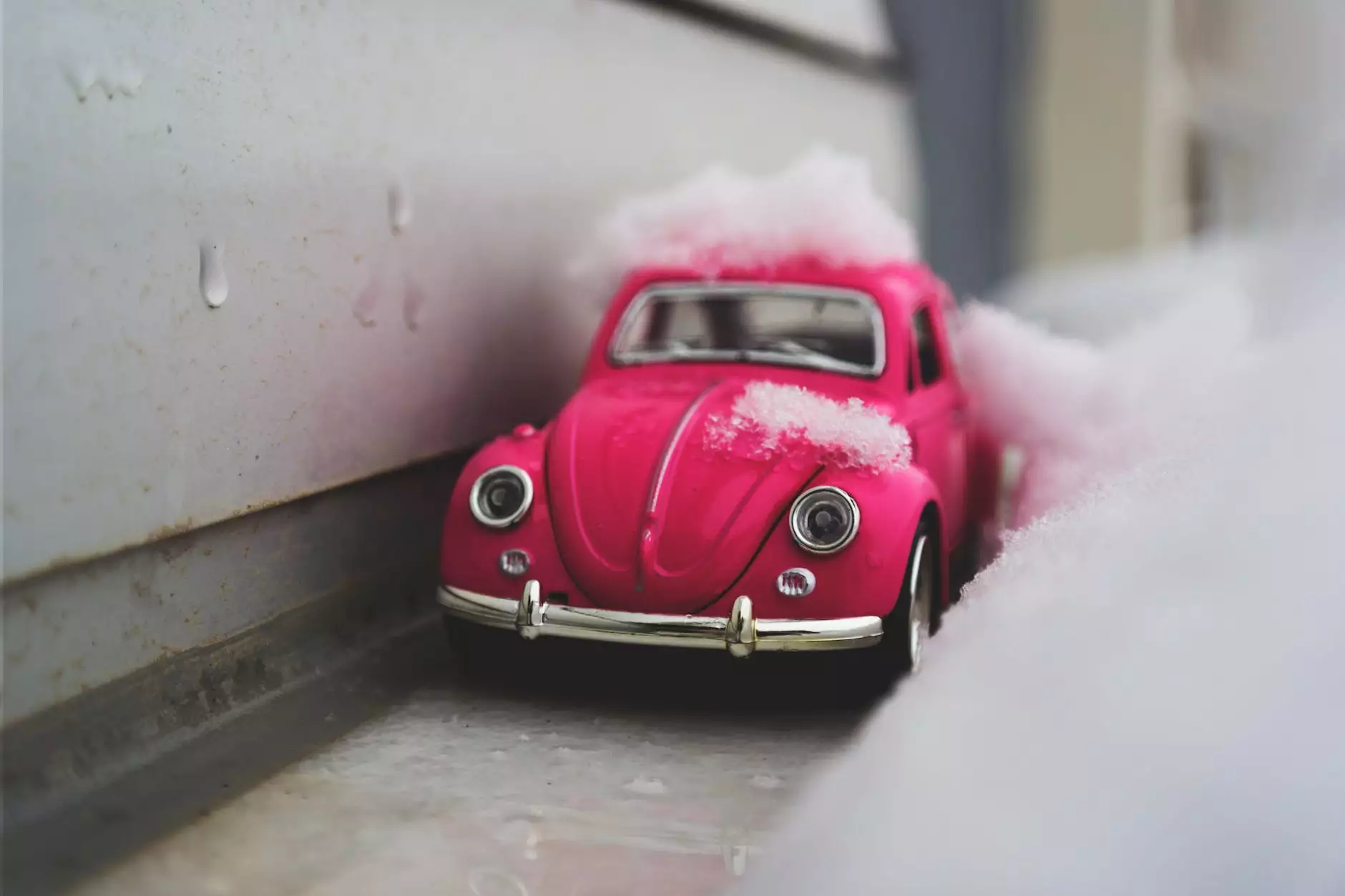
In the realm of metal fabrication, pressure die casting components have emerged as an essential process, significantly influencing the manufacturing landscape across various industries. This method not only boosts efficiency but also ensures the production of precise and intricate metal components. In this detailed guide, we will explore everything related to pressure die casting, including its processes, benefits, applications, and how businesses like Deep Mould leverage this technology to provide superior products.
What is Pressure Die Casting?
Pressure die casting is a metal casting process that involves the forcing of molten metal under high pressure into a mold cavity. This process is particularly suited for manufacturing small to medium-sized components with high levels of detail. The primary materials used in pressure die casting include aluminum, zinc, and magnesium alloys, known for their excellent mechanical properties and lightweight characteristics.
The Pressure Die Casting Process
The pressure die casting process can be broken down into several stages, each critical for ensuring high-quality components.
1. Mold Preparation
The first step in pressure die casting is the preparation of the die. Dies are usually made of high-quality steel and must be precisely machined to create the desired shape of the component. This precision ensures that the final product meets the specified dimensions and quality standards.
2. Melting the Metal
Next, the selected metal alloy is melted in a furnace. The temperature and atmosphere of the melting process are controlled to ensure minimal oxidation and contamination of the molten metal.
3. Injection of Molten Metal
Once the metal is melted, it is injected into the mold under high pressure, typically between 1000 to 2000 PSI. The high pressure forces the molten metal into every crevice of the mold, ensuring a complete fill and minimizing air pockets.
4. Cooling and Solidification
After the mold is filled, the molten metal is allowed to cool and solidify. Cooling times can vary based on the thickness of the component and the type of metal used.
5. Ejection of the Component
Once cooled, the die opens, and ejector pins push the newly formed component out of the mold. This stage must be handled delicately to prevent any damage to the freshly cast piece.
6. Finishing Processes
Finally, the component undergoes finishing processes, which may include machining, polishing, or painting, depending on the desired final appearance and functionality.
Advantages of Pressure Die Casting
Pressure die casting offers numerous advantages that make it a preferred choice among manufacturers:
- High Precision and Quality: Components produced through this method boast exceptional dimensional accuracy, tight tolerances, and a smooth surface finish.
- Efficiency: The process allows for high-volume production with minimal lead times, making it ideal for large scale applications.
- Versatility: It can accommodate a variety of alloys, expanding the use of this technique across different industries, such as automotive, aerospace, and consumer electronics.
- Reduced Waste: As the process employs a near-net-shape technology, it minimizes excess material and reduces post-production waste.
- Complex Geometries: The method allows for the creation of complex shapes that would otherwise be difficult to manufacture using traditional methods.
Applications of Pressure Die Casting
The versatility of pressure die casting extends to various industries. Some notable applications include:
1. Automotive Industry
In the automotive sector, pressure die casting is widely used to produce components such as engine blocks, transmission housings, and various other intricate parts. These components benefit from the high strength-to-weight ratio, essential for enhancing vehicle performance and fuel efficiency.
2. Aerospace Sector
The aerospace industry relies on pressure die casting for components that must meet stringent safety and performance standards. Parts such as landing gear, housings for electronic equipment, and brackets are commonly manufactured using this process.
3. Consumer Electronics
With the rapid advancement in consumer electronics, manufacturers utilize pressure die casting to produce lightweight and high-strength components such as housings for smartphones, laptops, and other gadgets.
4. Industrial Equipment
Industrial machines and equipment often require durable and precise components. Pressure die casting delivers the resilience and exact dimensions necessary for parts such as pump housings, gears, and valves.
The Role of Deep Mould in Pressure Die Casting
At Deep Mould, we are committed to leveraging our expertise in pressure die casting to deliver high-quality components tailored to our clients' specific needs. With state-of-the-art technology and a skilled workforce, we ensure that every component manufactured meets rigorous industry standards.
Quality Assurance
We believe that quality is paramount. Our rigorous quality assurance processes involve:
- Detailed inspections at every production stage.
- Advanced testing equipment to verify dimensional accuracy and material integrity.
- Adherence to international standards of manufacturing practices.
Continuous Improvement
Deep Mould invests in research and development, continuously enhancing our die casting methods to improve efficiency and reduce costs. Our approach ensures that we remain at the forefront of the industry, delivering innovative solutions to our clients.
Future Trends in Pressure Die Casting
The landscape of pressure die casting is constantly evolving. Some emerging trends include:
1. Automation and Industry 4.0
With the rise of Industry 4.0, automation in die casting processes is becoming more prevalent. Smart factories leverage IoT technologies to monitor manufacturing processes in real-time, enhancing efficiency and reducing error rates.
2. Sustainable Practices
As industries shift towards sustainability, pressure die casting processes are being optimized to minimize energy consumption and waste. Techniques such as recycled alloys and eco-friendly molding materials are gaining traction.
3. Advanced Alloys
Research into new metal alloys that exhibit superior properties is paving the way for even more innovative products. These advanced materials can offer enhanced strength, corrosion resistance, and lightweight characteristics, appealing to a broad spectrum of industries.
Conclusion: The Future of Pressure Die Casting Components
The world of pressure die casting components is vast, filled with opportunities for innovation and improvement. As industries continue to demand more precise, efficient, and sustainable manufacturing solutions, processes like pressure die casting will play an instrumental role. Companies like Deep Mould exemplify the potential of this technology by providing high-quality components that meet the evolving needs of various sectors.
By understanding the intricacies of pressure die casting, businesses can make informed decisions regarding their manufacturing processes, ultimately contributing to their success in a competitive marketplace. As we move forward, embracing new technologies and methodologies will be critical in maintaining leadership in the metal fabrication industry.