Understanding Injection Mold Manufacturing: A Comprehensive Guide
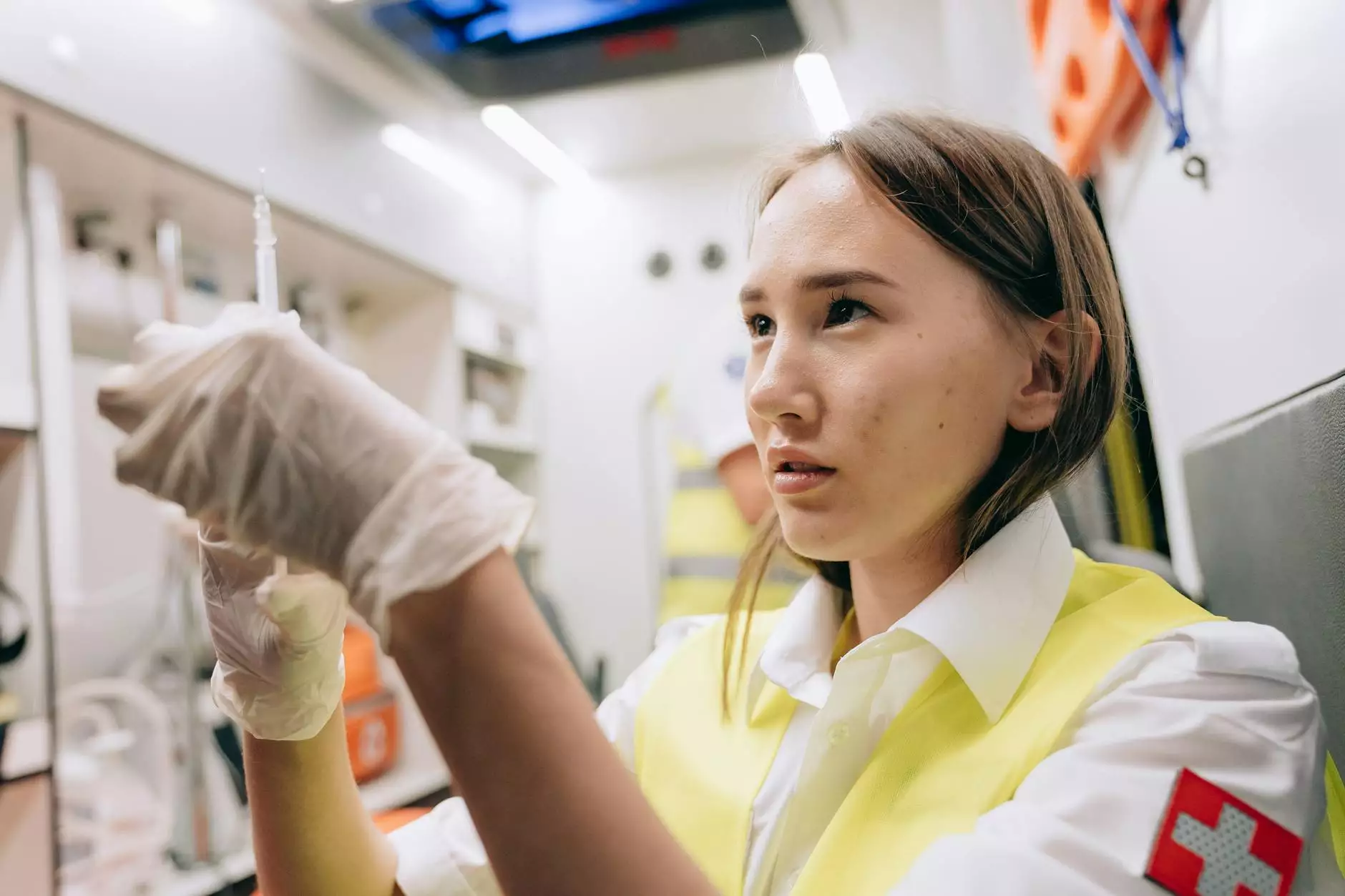
Injection mold manufacturing is a pivotal process that forms the backbone of numerous industries today. As businesses strive for efficiency and precision in production, the techniques and technologies surrounding injection mold manufacturing continue to evolve. This article delves deep into the essentials of injection mold manufacturing, revealing its significance, processes, applications, and the future it promises.
What is Injection Mold Manufacturing?
At its core, injection mold manufacturing is a manufacturing process used for producing parts by injecting material into a mold. The materials used typically include thermoplastics, thermosetting polymers, metals, and glass. This method is noted for its ability to produce high volumes of parts with excellent dimensional accuracy.
Historical Background
The roots of injection mold manufacturing can be traced back to the late 19th century. The first patent for the injection molding process was awarded in 1872, marking the beginning of a shift in manufacturing practices. As technology has progressed, so too have the methods and materials utilized in injection mold manufacturing, allowing for more intricate designs and increased efficiency.
The Benefits of Injection Mold Manufacturing
Injecting mold manufacturing offers a plethora of benefits, making it a preferred choice for manufacturers around the globe:
- High Efficiency: Once the mold is created, producing parts can be rapid, enabling high throughput levels.
- Consistency in Quality: The use of molds ensures that each part produced is identical, which is crucial for assembly lines.
- Cost-Effectiveness: While the initial investment in mold production may be high, the cost-per-part decreases significantly with volume.
- Complex Designs: Injection molds can create intricate designs that would be impossible or costly with other methods.
- Material Variety: A wide array of materials can be used, enhancing design possibilities and functionality.
Industry Applications
Injection mold manufacturing finds extensive applications across various sectors:
- Automotive: Components such as dashboards, bumpers, and clips.
- Consumer Goods: Containers, bottles, and household items.
- Medical Devices: Syringes, surgical instruments, and diagnostic equipment.
- Electronics: Housings for computers, phones, and other gadgets.
The Injection Molding Process Explained
The injection mold manufacturing process involves several stages:
1. Designing the Mold
The first step is to design the mold. This stage requires a deep understanding of the part to be produced and the materials to be used. Advanced software programs are often utilized to create detailed 3D models.
2. Creating the Mold
Once the design is complete, the mold is created, typically from steel or aluminum. The mold-making process can be intricate, requiring precision machining to ensure that every detail of the design is captured.
3. Injection
In this stage, material — usually in pellet form — is heated until it melts and then injected into the mold under high pressure. This process fills the mold completely, ensuring that all details are captured.
4. Cooling
After injection, the material must cool and solidify, which can involve passing cold water through the mold or using air cooling. Proper cooling ensures that the final product retains its dimensions accurately.
5. Ejection
Once cooled, the mold is opened, and ejector pins push the finished part out. This stage is crucial to prevent damage to the part.
Materials Used in Injection Mold Manufacturing
Choosing the correct material for injection mold manufacturing is essential, as it affects the performance of the final product. Here are some commonly used materials:
1. Thermoplastics
These are plastics that become pliable when heated and solidify upon cooling. They can be remolded multiple times, making them great for recycling. Popular types include:
- Polyethylene (PE): Durable and adaptable, used widely for containers.
- Polypropylene (PP): Resistant to fatigue and chemicals, ideal for automotive parts.
- Polyvinyl Chloride (PVC): Versatile, used in construction and electrical applications.
2. Thermosetting Plastics
These materials undergo a chemical change when molded, forming a rigid structure that cannot be remolded. Examples include:
- Epoxy: Strong binding properties, often used in electrical components.
- Phenolic: Known for heat resistance, used in automotive parts.
Challenges in Injection Mold Manufacturing
While injection mold manufacturing offers numerous advantages, it is not without its challenges. Some common issues include:
- Initial Costs: The cost of creating molds can be significant, which may deter small businesses.
- Complexity of Design: High intricacy in designs can increase lead times and costs.
- Material Limitations: Not all materials are suited for injection molding, which may limit design choices.
- Maintenance: Molds require regular maintenance to avoid defects in production.
The Future of Injection Mold Manufacturing
As the landscape of manufacturing evolves, the future of injection mold manufacturing looks promising:
1. Advancements in Technology
With the integration of technologies such as automation, robotics, and artificial intelligence, injection mold manufacturing is becoming more efficient. These advancements enable faster production and reduce the potential for human error.
2. Sustainable Practices
As industries shift towards sustainability, the focus on eco-friendly materials and processes in injection mold manufacturing is intensifying. Biodegradable thermoplastics and energy-efficient molding processes are gaining traction.
3. Customization and Precision
The demand for customized products is rising, pushing manufacturers to adopt flexible production techniques that allow for small batch sizes while maintaining precision.
Conclusion
Injection mold manufacturing is a critical component of modern production processes, affecting various sectors from automotive to consumer goods. Its efficiency, cost-effectiveness, and ability to produce complex designs make it an indispensable technique for manufacturers globally. As advancements continue, the industry is poised to embrace even greater innovations, ensuring that injection mold manufacturing remains at the forefront of manufacturing technologies. With companies like deepmould.net leading the charge, the future of this industry holds exciting prospects for businesses and consumers alike.